I mentioned in another post that I attempt to scratch built a dungeon interior to go with my miniatures. Yesterday I had a nice idea how to get away from boring wall segments and make the dungeon more appealing to the eye.
As I am painting a dwarven warrior at the moment I thought about where they would store their beer and naturally, a dark place like a dungeon would be well suited for this purpose.
Well, I guess I am more thinking of Moria where all of the dwarves are already dead and only remnants of life are still visible. The plan is thus to have a wall segment that also resembles a wine or beer storage, complete with oaken barrels.
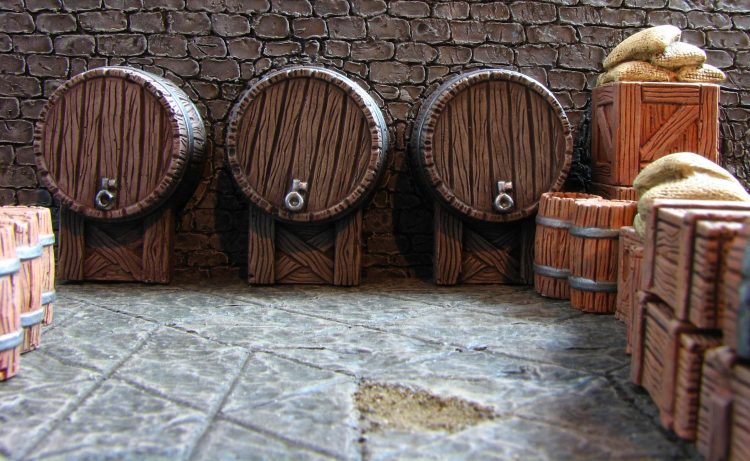
Hirst Arts to the rescue
I own the Hirst Arts Cavern accessory mold (Nr. 85) which conveniently allows to cast half of a barrel with a wooden support structure. While Hirst Arts molds are not cheap, they pay off if you have a more ambitious project in mind, where a lot of architectural elements and accessories are needed. I can only recommend the mold, as it gives you all dungeon dressings you may need: Treasure piles, chests, crates, big and small barrels, levers, torches, wall adornments, crystals, buckets etc.
I use Hydrocal to cast the pieces and they come out durable and with minimal casting artefacts. For the wall segment I decided to try out some new material, a block of Original Sculpey.
Sculpting the wall
To form the clay you obviously need some sculpting tools. I got a selection of tools from a shop that sells sculpting supplies.
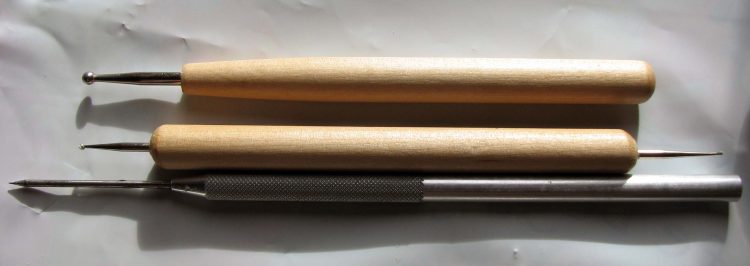
I took a bit of clay and rolled it out on a sturdy plastic bag. I aimed for around 5mm thickness, so that I can later glue it on a piece of styrofoam to save clay and weight. Surprisingly it did not stick much, but I guess a piece of glass would be much better, as you can directly transfer your piece into the oven .
After I traced the size of the wall segment, I started carving the brick pattern. I already encountered a small problem with the Sculpey: It is very soft and tends to drag a bit. I guess it is a matter of practise. Cooling the clay also helps.
I transferred the finished wall to a metal sheet and followed the baking instructions. 15min turned out to be a bit short and I ended up baking it for 30 minutes. After baking, the Sculpey remained slightly flexible and has a rubbery feel to it.
Painting the wall
I proceeded with painting the piece and encountered no problems. The material takes acrylic paint well and keeps its shape. I was even able to slightly sand the piece. I started with a dark grey with a bit of brown mixed in (I use cheap acrylic wall paint for terrain building) and then drybrushed with gradually lighter shades.
Finally I applied a mixture of matt varnish, brown pigment and water (about 4 brush loads of varnish, one brush load of water and two small brush loads of pigment). This basically takes away any sheen and also provides some definition for the cracks and lines.
It took quite some time, but in the end I think it was worth it. In comparison to a wall made entirely out of styrofoam I would say the Sculpey provides much more definition and crisper lines, but judge for yourselves.
So far, so good. Now I have to finish painting the barrels, cast two more and glue the segment on a piece of styrofoam.
Wel done 🙂
Thank you for your comment. The Dungeon project is quite fun, but surely not as complex as your graveyard one.